The electronic weighing module is a practical and versatile accessory designed to work with sensors. It can be easily mounted on various types of containers, making it highly portable and adaptable. This module can be integrated into a complete weighing system, offering flexibility in installation and cost-effectiveness. Due to its ease of assembly and relatively low cost, it has become an essential component in many industrial applications, especially in chemical companies, where it is widely used and appreciated.
**First, Understanding the Weighing Module and Its Features**
**1. Introduction to the Weighing Module**
A weighing module is a structural accessory that works in conjunction with a sensor to measure weight accurately. It typically consists of a top plate, a base plate, a load cell, support columns, and mounting bolts. Depending on the design of the support column and top plate, there are three main types: fixed, semi-floating, and floating modules. In a typical weighing system, these modules are often used in sets—either three or four points—to provide stable support for different types of equipment. Whether it's a tank, hopper, or reaction vessel, the weighing module can be installed quickly and effectively, turning any container into a functional weighing system.
**2. Key Features of the Weighing Module**
Compared to traditional electronic scales, the weighing module offers several advantages. It is not limited by space, allows for flexible installation, and is easy to maintain. Unlike ground scales that require a dedicated platform, the weighing module is installed directly at the support points of the container, saving valuable floor space. This makes it ideal for environments where multiple containers are placed closely together.
Additionally, the weighing module allows for customizable range and resolution settings, which can be adjusted based on the specific needs of the application. If a sensor is damaged, it can be replaced without removing the entire module, reducing downtime and maintenance costs. The simple structure of the module also means that the overall investment required for a weighing system is relatively low, making it a cost-effective solution for many industries.
**Second, Applications of Weighing Modules in Chemical Enterprises**
**1. Use in Material Measurement**
Chemical companies rely heavily on storage and metering tanks during production and material handling. One common challenge is accurately measuring the weight of materials. Traditional methods such as rulers or flow meters measure volume and convert it to weight using density, which can introduce errors due to temperature changes or other factors. Mass flow meters are more accurate but are often too expensive for general use. The electronic weighing module offers a more economical and reliable alternative by directly measuring the weight of the material, ensuring greater accuracy and consistency.
**2. Application in Liquid Level Indication and Control**
Liquid level is a critical parameter in chemical processes. Conventional methods involve converting liquid level signals into electrical or pneumatic signals for control systems. However, this approach can lead to inaccuracies caused by changes in density or blockages from crystallization or clogging. Additionally, sensors in direct contact with corrosive media may require expensive materials, increasing costs. The weighing module avoids these issues by not coming into direct contact with the medium. It can be connected to recorders or controllers via analog output, enabling automated monitoring and control.
**3. Use in Processes Requiring Precise Material Amounts**
Some chemical processes demand precise control over the amount of material being added. Traditionally, this is done by placing a metering tank directly on the ground, which requires lifting equipment for calibration and inspection. Using an electronic weighing module eliminates this inconvenience, as the tank itself acts as the scale body, simplifying maintenance and improving operational efficiency.
**Third, Considerations for Purchasing, Installing, and Debugging the Weighing Module**
**1. Purchase Options**
When purchasing a weighing module, the number of modules (typically 3 or 4) should be chosen based on the number of support points on the container. Factors such as the weight of the container, potential vibrations, and loading conditions must be considered. A general rule for multi-sensor static weighing systems is to ensure that the total load (fixed + variable) does not exceed 70% of the sensor’s rated capacity multiplied by the number of sensors. This accounts for shocks, vibrations, and partial loads.
It’s also important to check if explosion-proof sensors are required, especially in environments where flammable or explosive substances are present.
**2. Installation Tips**
- Ensure proper horizontal alignment for both individual modules and the entire set.
- Avoid passing current through the sensor during welding; connect the ground wire to the scale body when welding the top plate and to the foundation when welding the bottom plate.
- If there are conveying pipes on the scale body, replace them with hoses or make the connecting pipes as long as possible to prevent interference with the sensor.
- Weld a calibration platform onto the container for testing purposes, as there may not be enough space to place weights directly on the container.
- Protect the junction box from moisture and seal any unused holes. If installed outdoors, a protective enclosure is necessary to prevent damage from rain. Moisture-related failures in the junction box should be taken seriously to avoid system downtime.
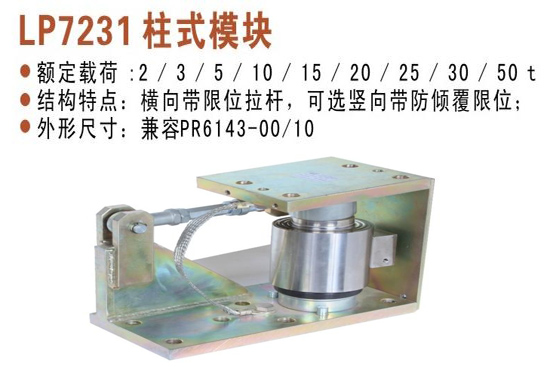
Water-Saving Makeup Cotton,Makeup Cotton,Dry Wet Cotton Pads,Wet Cotton Pad
COTTONWHISPER (TAIZHOU) DAILY PRODUCTS CO.,LTD , https://www.cottonwhipershop.com