The basic processes of lead-free soldering assembly include: a. Lead-free PCB manufacturing process; b. 96.5Sn / 3.5Ag and 95.5Sn / 4.0Ag / 0.5Cu eutectic and near-eutectic alloy systems used in solder paste; 99.3Sn / 0.7Cu eutectic alloy system for wave soldering applications; d. 99.3Sn / 0.7Cu alloy system for manual welding. Although these are all feasible processes, there are still several major problems in the implementation. For example, the raw material cost is still higher than the standard Sn / Pb process, the restriction on the humidity has been increased, and it is required to maintain the inert air state in the wave soldering process To have a sufficient amount of nitrogen) and may raise the reflow temperature to the limit temperature range (235 ~ 245 ℃) and increase the thermal requirements of various components and so on. As far as lead-free alternatives are concerned, there is currently no set of generally accepted specifications. After many discussions with many professionals in this field, we have come up with the following technical and application requirements: Metal prices Many assembly manufacturers require lead-free The price of the alloy cannot be higher than 63Sn / 37Pb, but unfortunately all existing lead-free alternatives cost at least 35% higher than 63Sn / 37Pb. When choosing lead-free electrodes and solder wires, metal cost is the most important factor; and when making solder paste, because the technical cost accounts for a relatively high proportion of the overall manufacturing cost, it is not so sensitive to the price of metal . Melting point Most assembly manufacturers (not all) require a minimum solid phase temperature of 150 ° C in order to meet the operating temperature requirements of electronic equipment, and the maximum liquid phase temperature depends on the specific application. Electrode for wave soldering: In order to successfully implement wave soldering, the liquid phase temperature should be lower than the furnace temperature by 260 ° C. Solder wire for manual / machine welding: The liquid phase temperature should be lower than the working temperature of the soldering iron tip by 345 ° C. Solder paste: The liquid phase temperature should be 250 ℃ lower than the reflow temperature. For many existing reflow ovens, this temperature is the limit of practical temperature. Many engineers require that the maximum reflow temperature should be lower than 225 ~ 230 ℃, but there is no feasible solution to meet this requirement. It is generally believed that the closer the alloy reflow temperature is to 220 ° C, the better the effect is. It is ideal to avoid higher reflow temperatures because it can minimize the damage to the components and minimize the impact on special components. Requirements, at the same time, it can also minimize the discoloration and warpage of the circuit board, and avoid excessive oxidation of the pads and wires. Good conductivity This is the basic requirement for electronic connections. Good thermal conductivity In order to dissipate heat, the alloy must have rapid heat transfer capability. Small solid-liquid coexistence temperature range Non-eutectic alloys will solidify in a temperature range between the liquid phase temperature and the solid phase temperature. Most metallurgical experts recommend that this temperature range be controlled within 10 ℃ in order to form a good Solder joints to reduce defects. If the alloy solidification temperature range is wide, cracking of the solder joints may occur, prematurely damaging the equipment. Low-toxic alloys and their components must be non-toxic, so this requirement excludes cadmium, thallium, and mercury from consideration; some people also require that by-products derived from toxic substances cannot be used, and therefore bismuth is excluded because bismuth is mainly From the by-product of lead extraction. Has good solderability. Under the conditions of existing equipment and no-clean flux, the alloy should have sufficient wettability and can be used with conventional no-clean flux. Because the cost of inert treatment of the wave crest is not too high, it is acceptable to use the conditions of wave soldering plus inert environment; but for SMT reflow soldering, the alloy should preferably have the ability to reflow soldering in air, because of the reflow The inert treatment of the welding furnace is costly. Good physical properties (strength, stretch, fatigue, etc.) The alloy must be able to provide the mechanical strength and reliability that 63Sn / 37Pb can achieve, and no protruding fillet welds (especially (Alloys with a larger solid-liquid temperature range). The production repeatability / melting point consistency electronic assembly process is a high-volume manufacturing process, which requires that its repeatability and consistency be maintained at a high level. The melting point changes greatly due to changes in composition during mass production and cannot be considered. Alloys composed of more than three components often undergo separation or composition changes, making the melting point unstable. The higher the complexity of the alloy, the greater the possibility of changes. Solder joint appearance The appearance of solder joints should be close to tin / lead solder. Although this is not a technical requirement, it is a practical need to accept and implement alternatives. Supply capacity When trying to find a solution for the industry, we must consider whether the material has sufficient supply capacity. From a technical point of view, indium is a very special material, but if you consider the global supply capacity of indium, people will soon completely exclude it from the scope of consideration. In addition, the industry may prefer a standard alloy system rather than a dedicated system. Standard alloys have wider access channels, so prices will be more competitive, and special alloy supply channels may be restricted, so material prices will increase significantly. Compatibility with lead Since short-term will not be immediately converted into a lead-free system, lead may still be used on the terminals of certain components or the pads of printed circuit boards. Some lead-containing alloys have a very low melting point, which reduces the strength of the connection. For example, the melting point of a certain bismuth / tin / lead alloy is only 96 ° C, which greatly reduces the welding strength. Metal and alloy selection Among various candidate lead-free alloys, tin (Sn) is used as the base metal because of its low cost, sufficient supply, and ideal physical properties, such as electrical conductivity / thermal conductivity and wettability, It is also the base metal of 63Sn / 37Pb alloy. Other metals commonly used with tin include silver (Ag), indium (In), zinc (Zn), antimony (Sb), copper (Cu), and bismuth (Bi). The reason for choosing these materials is that when they form an alloy with tin, they generally lower the melting point and obtain ideal mechanical, electrical and thermal properties. Table 1 lists the cost, density, annual production capacity and supply of various metals. In addition, when investigating the supply capacity of materials, the results will be clearer when the dosage factors are added together for comprehensive consideration. For example, the annual consumption of 63Sn / 37Pb in the electronics industry is about 45,000 tons, of which about 16,000 tons are used in North America. At this time, as long as 3% of the assembly plants in North America use tin / indium lead-free alloys containing 20% ​​indium, Its indium consumption will exceed the global production capacity of the metal. In the past five years, the industry has launched a series of alloy composition recommendations and evaluated these lead-free alternatives. The total number of alternatives exceeds 75, but the main options can be summarized as less than 15. In the face of all candidate alloys, we use some technical specifications to narrow the selection to a smaller range for easy selection. Indium Indium may be the most effective component to lower the melting point of tin alloys, and it also has very good physical and wetting properties, but indium is very rare, so large-scale applications are too expensive. For these reasons, indium-containing alloys will be excluded from further consideration. Although indium alloy may be a better choice in some specific occasions, it is not suitable for the entire industry. In addition, differential scanning calorimetry also shows that the melting point of 77.2Sn / 20In / 2.8Ag alloy is very low, only 114 ℃, so it is not suitable for some applications. Zinc Zinc is very cheap, almost the same price as lead, and is readily available. It also has a very high efficiency in reducing the melting point of tin alloys. As far as zinc is concerned, its main disadvantage is that it will react quickly with oxygen to form stable oxides. In the wave soldering process, the result of this reaction is to produce a large amount of tin slag, and the more serious is the stable oxidation formed It will cause the wettability to become very poor. Perhaps these technical obstacles can be overcome by inertization or special flux formulations, but now people are demanding a demonstration of zinc-containing solutions in a larger process range, so zinc alloys will also be excluded in future considerations. Bismuth has a significant effect on lowering the solid phase temperature of the tin alloy, but it has no such effect on the liquid phase temperature, so it may cause a larger solid-liquid coexistence temperature range, and a too large solidification temperature range will cause the solder legs to rise. Bismuth has very good wetting properties and good physical properties, but the main problem of bismuth is that the melting point of the alloy formed by tin / bismuth alloy after encountering lead will be relatively low, and the component pin or the pad of the printed circuit board There will be lead on it. The melting point of tin / lead / bismuth is only 96 ℃, which is easy to cause solder joint breakage. In addition, the supply capacity of bismuth may be reduced due to the limitation of lead output, because bismuth is still mainly extracted from the by-products of lead. If the use of lead is restricted, the output of bismuth will be greatly reduced. Although we can also obtain bismuth by direct mining, this cost will be relatively high. For these reasons, bismuth alloys are also excluded. Four- and five-component alloys Alloys composed of four or five metals provide us with a series of alloy composition combinations, and the possibilities are endless. Compared with bimetallic alloy systems, most four- or five-metal alloys can significantly reduce the solid-phase temperature, but may not do anything to lower the liquidus temperature, because most four- or five-metal alloys are not eutectic materials, which means Different metallographic forms will be formed at different temperatures, and as a result, the reflow temperature cannot be lower than that required by simple bimetallic systems. Another problem is that the alloy composition often changes, so the melting point will also change, which is often encountered in four or five metal alloys. It is difficult for an alloy composed of three metals to achieve "same batch" and "batch-by-batch" consistency in the tin powder in solder paste, and to achieve the same consistency in an alloy composed of four and five metals. Its complexity and difficulty Bigger. Therefore, multi-component alloys will be excluded from further consideration unless certain multi-component alloy components have better characteristics than binary systems. But for now, the industry has not found any four- or five-metal alloys that are better than binary or ternary alternatives (whether in terms of cost or performance). Table 2 lists some of the main lead-free alternatives, and the reasons for the final selection or non-selection. The table includes unit weight price, unit volume price (for solder paste, unit volume price is more cost-effective), and melting point, etc., These alloys are arranged in increasing order of their liquidus temperatures. The suitable alloys are now individually selected according to the specific requirements of each welding application. First consider the electrode (wave soldering) and wire (manual and machine welding). Requirements for electrodes for wave soldering include: a. Continuous welding at a maximum furnace temperature of 260 ° C; b. Fewer welding defects (missing soldering, bridging, etc.); c. Cost as low as possible; d. No overproduction More welding slag. As a result, all the selected alloys meet the requirements of wave soldering, but 99.3Sn / 0.7Cu and 95Sn / 5Sb alloys can save more cost than other alternatives. In comparison, the liquid phase temperature of 99.3Sn / 0.7Cu is 13 ℃ lower than that of Sn / Sb alloy, so 99.3Sn / 0.7Cu becomes the best candidate for wave soldering. The requirements for manual soldering tin wires are very similar to the above electrode applications. Cost considerations are still a priority, and they also require better wetting and soldering capabilities. The alloy for soldering wire must be able to be easily drawn into a wire, and can be soldered with a soldering iron tip of 345 to 370 ° C. 99.3Sn / 0.7Cu alloy can meet these requirements. Compared with welding rods and wires, solder paste is less concerned about alloy cost, because metal cost accounts for less of the total cost of manufacturing process using solder paste. The main requirement for choosing solder paste alloy is to minimize the reflow temperature. Looking at the alloys listed in the table, it can be found that the liquid phase temperature is the lowest 95.5Sn / 4.0Ag / 0.5Cu (melting point 217 ~ 218 ℃) and 96.5Sn / 3.5Ag (melting point 221 ℃). These two alloys are more suitable choices and have their own characteristics. In contrast, Sn /
Click to enter the booth of Beijing Kehai Venture Science and Trade Co., Ltd. to see more I want to submit
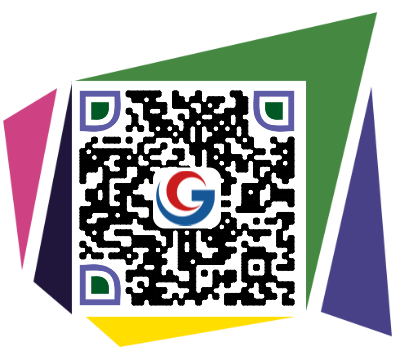
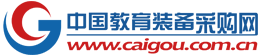
Sweep, welcome attention
Official WeChat of Educational Equipment Procurement Network
Master the latest and most authoritative information in the education equipment industry
Copyright and Disclaimer:
â‘ The copyright of all works on this website that indicate "Source: China Education Equipment Purchasing Network" belongs to China Education Equipment Purchasing Network, and may not be reproduced, edited or used in other ways without authorization from this website. Works that have been authorized by this website should be used within the scope of authorization, and indicate "Source: China Education Equipment Purchase Network". Violators of this website will be held accountable for legal liabilities.
â‘¡ All works on this website that indicate "Source: XXX (non-this website)" are reproduced from other media. The purpose of this reprint is to transmit more information. This does not mean that this website agrees with its views and is responsible for its authenticity. Take direct responsibility and joint liability for infringement of such works. If other media, websites or individuals download and use it from this website, they must keep the "source of the manuscript" indicated on this website, and bear the legal responsibility of copyright and other.
â‘¢ If the content of the work, copyright and other issues are involved, please contact this website within two weeks from the date of publication of the work, otherwise it is deemed to waive the relevant rights.
Shandong Dyehome Intelligent Equipment Co.,Ltd(Company NEEQ STOCK CODE:836635)
The cooling time of special PP belt can adjust according to the customer's need, so that every PP belt packing can adhere perfectly.
If the devices of saving electricity can't pack continually and the motor will automatically stop revolving, reduce wear and increase the life of the machine after 60 seconds.
Using the most advanced PCB microchip circuit board to control, have low failure rate and easy to maintain.
Our product can heat easily without electric heating piece and improve work efficiency.
The control panel with the tape feed switch and cutting switch make the operation more convenient.
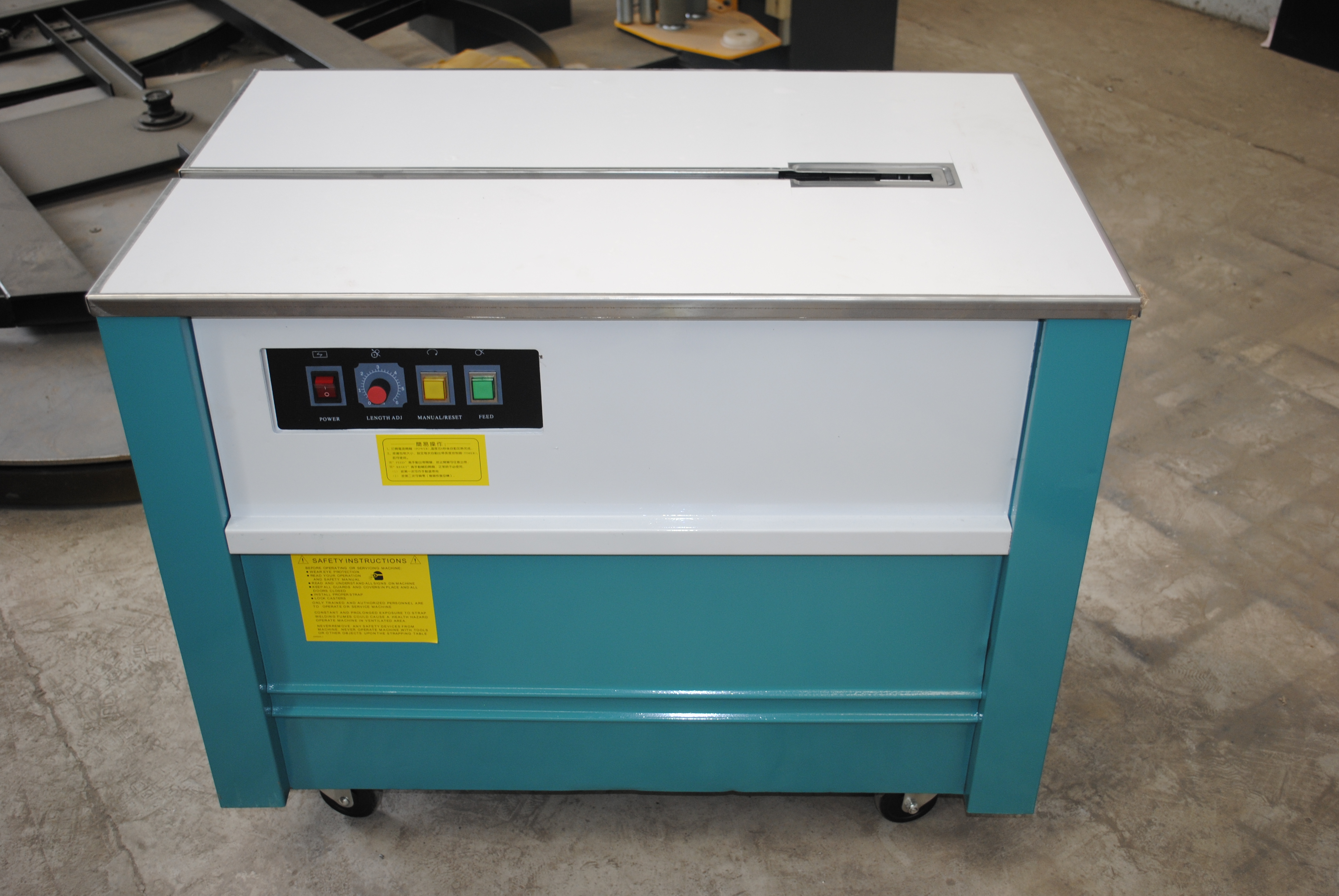
Semi-auto Strapping Machine
Semi-Auto Strapping Machine,Semi-Auto Pallet Strapping Machine,Low-Table Semi-Auto Strapping Machine,Semi-Automatic Strapping Machine
Shandong Dyehome Intelligent Equipment Co., Ltd. , https://www.dyehomepack.com